Finding Failures Before They Cause Shut Downs
How Ponderay Newsprint Company Inspects Moving Parts
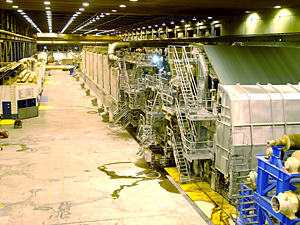
Ponderay Newsprint Company of Usk, Washington, meets its annual production of up to 260,000 metric tonnes of newsprint on a single 330” trim Valmet Twin Wire Paper Machine. To supply the partnership that formed Ponderay—between AbitibiBowater Inc. (Ponderay’s managing partner) and subsidiaries of five newspaper publishers—Perry Pearman, Reliability Engineer at Ponderay, wants to “increase production reliability for a competitive advantage.”
Beginning about three years ago, Pearman says he was asked to build a program to address this issue. A major problem for reliability was “How do you look at machinery that is moving rapidly and determine where there is failure before there is break down?” The Mill has countless pumps, motors, belts, agitators, motor couplings, and fans. Break down of even a single motor, pump or belt can shut down the entire football field-sized machine.
Joel Hendershott, Operations Technician 2, described by Perry as “the resident plant genius,” was pulled into the project. Hendershott says he worked with machine operators to devise inspection routes, ensuring that “each piece of equipment is checked on a weekly basis.” This became the Operator Driven Reliability Program.
About 28 routes were developed, examining equipment from the basement to platforms above the machine. In order to see the condition of moving parts, a strobe light was needed to provide a “stop-action” effect.
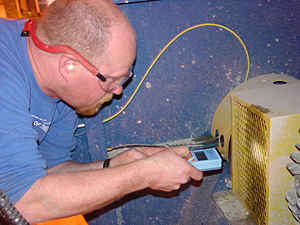
In a search of the Internet, Hendershott came across Nobaki’ ESL 10-A LED Stroboscope. “It was exactly what we needed—small, light and simple to use for on-the-run inspections with LED’s that don’t burn out.” According to Hendershott, “It’s very easy to read on the run and it comes at a better price than other strobes. And the Hoto LED stroboscope fits into pouches which leaves the operators’ hands free.” This is especially useful as operators climb up or down or into various areas to get a look at their assigned pieces of machinery.
To accommodate the use of the strobe, belt and rotating shaft guards were modified with cutaways that were then covered in black wire mesh. This meant that as operators directed the strobe on the moving parts, the dark mesh provided a higher level of contrast for ease of viewing. This contrast makes, for example, grease stains thrown by loosening bolts more visible.
Pearman says, “The push button speed control on the Hoto LED strobe is just what we needed. By pressing the button, operators can change the speed of the strobe, highlighting different sections of a rotating shaft. Then they can see all sides of a coupling.” This is crucial when some couplings have a six-year shelf life. In addition, Hendershott says that by changing the speed of the strobe while inspecting a belt, “fraying, bad splices and missing chinks can be discovered before the belts fly apart.”
Electricians or maintenance personnel can provide a more expert opinion, as needed. For example, Pearman says, “Greg Vaughn, the Mill Electrical Engineer, and I grabbed strobes to look at the motor end bell cooling systems. In the end bell, a fan pushes cool air over motor cooling fins. For every 18 degrees of increased motor temperature, you decrease the life of the motor by 50%.” While using the strobes to inspect the cleanliness of the fan blades, Perry and Greg were able to see if the fan blades were damaged or had broken off. This will lead to premature motor failures.
Hendershott feels that the Hoto LED strobes were critical for the project. “You know, I don’t think the Operator Driven Reliability Program would be working if we hadn’t been able to find the right strobes. The Hoto LED strobes make looking at our moving machinery a go.”
The operator checks are part of an overall Basic Care and Condition Monitoring Program at Ponderay Newsprint Company. After failure is noted, the operators generate red- or yellow-flagged repair orders and schedule repairs for the next outage. This data and data on conditions throughout the plant are shared with several mills in an effort to problem solve within the industry rather than within a single plant.